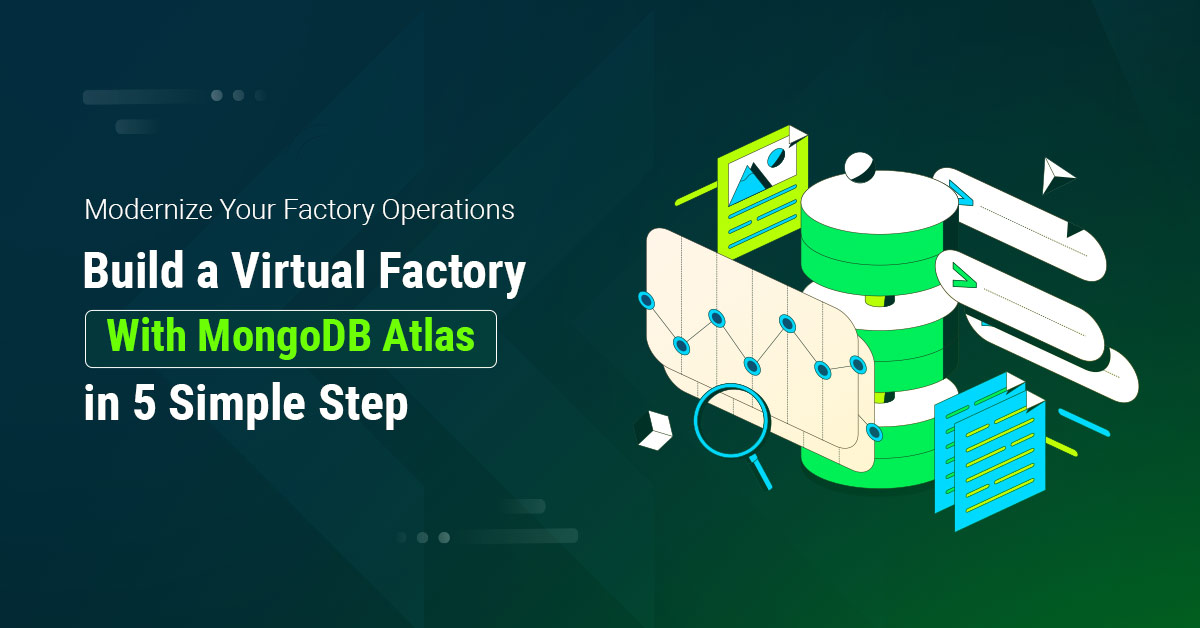
Virtual factories are revolutionizing the manufacturing landscape. Coined as the “Revolution in factory planning” by BMW Group at NVIDIA, this cutting-edge approach is transforming the way companies like BMW and Hyundai operate, thanks to groundbreaking partnerships with technology companies such as NVIDIA and Unity. At the heart of this revolution lies the concept of virtual factories, computer-based replicas of real-world manufacturing facilities. These virtual factories accurately mimic the characteristics and intricacies of physical factories, making them a powerful tool for manufacturers to optimize their operations. By leveraging AI, they unlock a whole new world of possibilities, revolutionizing the manufacturing landscape, paving the way for improved productivity, cost savings, and innovation.
In this blog we will explore the benefits of virtual factories and guide you through the process of building your own virtual factory using MongoDB Atlas. Let’s dive in!
Unlocking digital transformation
The digitalization of the manufacturing industry has given rise to the development of smart factories. These advanced factories incorporate IoT sensors into their machinery and equipment, allowing workers to gather data-driven insights on their manufacturing processes. However, the evolution does not stop at smart factories automating and optimizing physical production. The emergence of virtual factories introduces simulation capabilities and remote monitoring, leading to the creation of factory digital twins, as depicted in Figure 1.
By bridging the concepts of smart and virtual factories, manufacturers can unlock greater levels of efficiency, productivity, flexibility, and innovation.
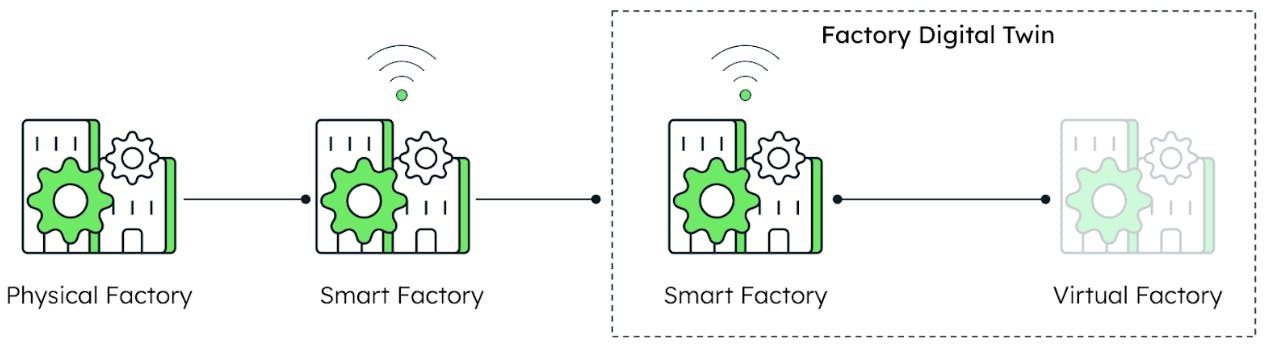
Leveraging virtual factories in manufacturing organizations provides many benefits including:
- Optimization of production processes and identification of inefficiencies. This can lead to increased efficiency, reduced waste, and improved quality.
- Aiding quality control by contextualizing sensor data with the manufacturing process. This allows analysis of quality issues and implementation of necessary control measures while dealing with complex production processes.
- Simulating manufacturing processes and testing new products or ideas without the need for physical prototypes or real-world production facilities. This significantly reduces costs associated with research and development and minimizes the risk of product failure.
However, setting up a virtual factory for complex manufacturing is difficult. Challenges include managing system overload, handling vast amounts of data from physical factories, and creating accurate visualizations. The virtual factory must also adapt to changes in the physical factory over time. Given these challenges, having a data platform that can contextualize all the data coming in from the physical factory and then feed that to the virtual factory and vice versa is crucial. And that is where MongoDB Atlas, our developer data platform, comes in, providing synchronization capabilities between physical and virtual worlds, enabling flexible data modeling and providing access to the data via a unified query interface as seen in Figure 2.
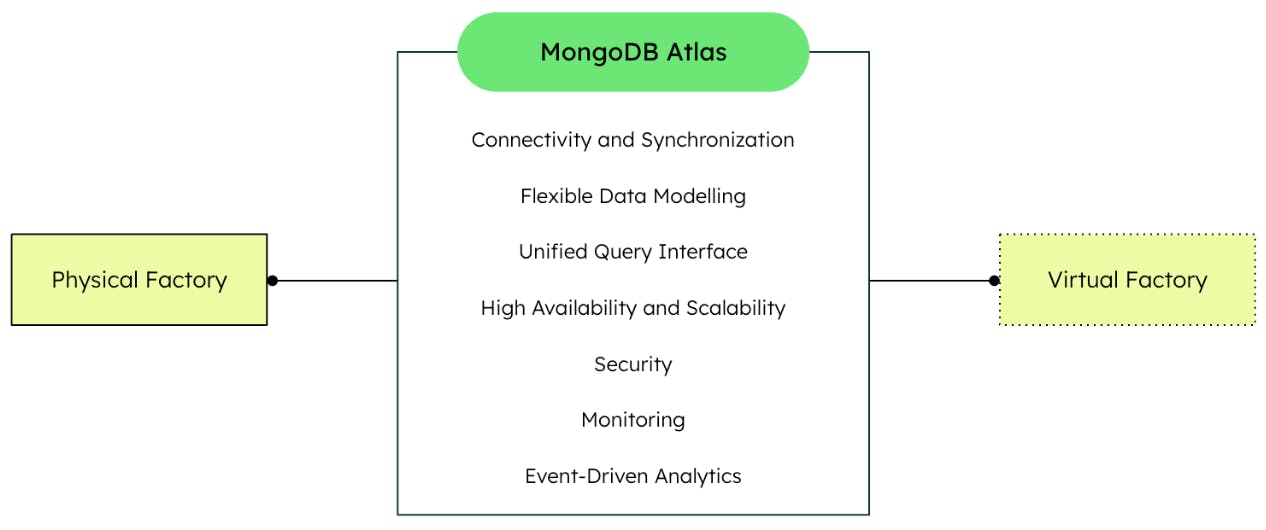
Now that we’ve discussed the benefits and the challenges of building virtual factories, let’s unpack how simple it is to build a virtual factory with MongoDB Atlas.
How to build a virtual factory MongoDB Atlas
1. Define the business requirements
The first step of the process is to define the business requirements for the virtual factory. Our team at MongoDB uses a smart factory model from Fischertechnik to demonstrate how easily MongoDB can be integrated to solve the digital transformation challenges of IIoT in manufacturing. This testbed serves as our foundational physical factory and the starting point of this project.
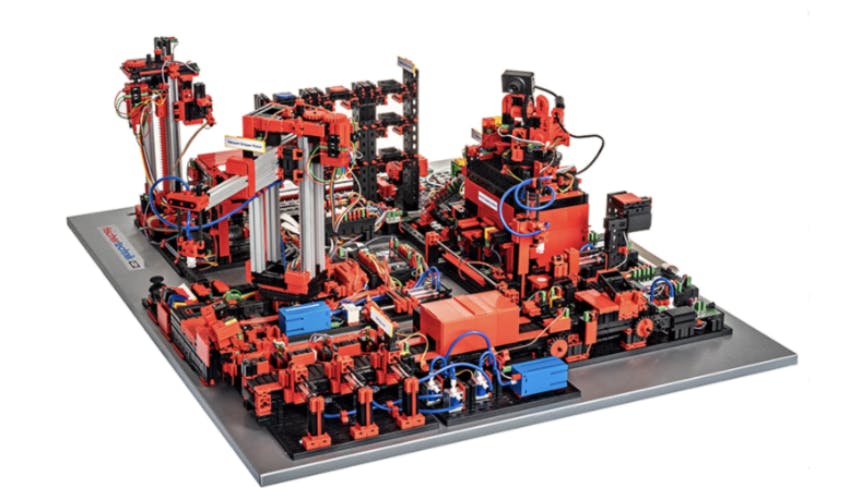
We defined our set of business requirements as the following:
- Implement a virtual run of the physical factory to identify layout and process optimizations.
- Provide real-time visibility of the physical factory conditions such as inventory for process improvements.
This last requirement is critical; while standalone simulation models of factories can be useful, they typically do not take into account the real-time data from the physical factory. By connecting the physical and virtual factories, a digital twin can be created that takes into account the actual performance of the physical factory in real-time. This enables more accurate predictions of the factory’s performance, which improves decision-making, process optimization, and enables remote monitoring and control, reducing downtime and improving response times.
2. Create a 3D model
Based on the previous business requirements, we created a 3D-model of the factory in a widely used game engine, Unity. This virtual model can be visualized using a computer, tablet or any virtual reality headset.
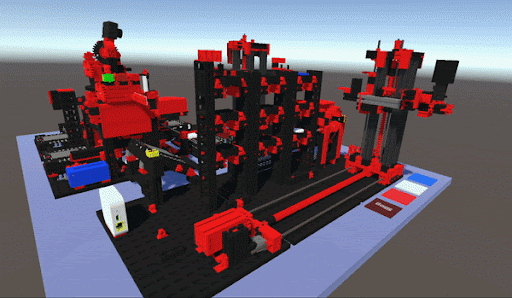
Additionally, we also added four different buttons (red, white, blue, and “stop”) which enables users to submit production orders to the physical factory or stop the process altogether.
3. Connect the physical and virtual factories
Once we created the 3D model, we connected the physical and virtual factories via MongoDB Atlas. Let’s start with our virtual factory software application. Regardless of where you deploy it, be it a headset or a tablet, you can use Realm by MongoDB to present data locally inside Unity and then synchronize it with MongoDB Atlas as the central data layer. Allowing us to have embedded databases where there’s resource constrainment and MongoDB Atlas as a powerful and scalable cloud backend technology.
And lastly, to ensure data synchronization and communication between these two components, we leveraged MongoDB Atlas Device Sync, providing bi-directional synchronization mechanism and network handling.
Now that we have our virtual factory set-up, let’s have a look at our physical one.
In a real manufacturing environment, many of the shopfloor connectivity systems can connect to MongoDB Atlas and for those who don’t natively, it is very straightforward to build a connector. At the shopfloor layer you can have MongoDB set up so that you can analyze and visualize your data locally and set up materialized views. On the cloud layer, you can push data directly to MongoDB Atlas or use our Cluster-to-Cluster Sync functionality.
A single IoT device, by itself, does not generate much data. But as the amount of devices grows, so does the volume of machine-generated data and therefore the complexity of the data storage architecture required to support it. The data storage layer is often one of the primary causes of performance problems as an application scales. A well-designed data storage architecture is a crucial component in any IoT platform.
In our project, we have integrated AWS IoT Core to subscribe to MQTT messages from the physical factory. Once these messages are received and filtered, they are transmitted to MongoDB Atlas via an HTTP endpoint. The HTTP endpoint then triggers a function which stores the messages in the corresponding collection based on their source (e.g., messages from the camera are stored in the camera collection). With MongoDB Atlas, as your data grows you can archive it using our Atlas Online Archive functionality.
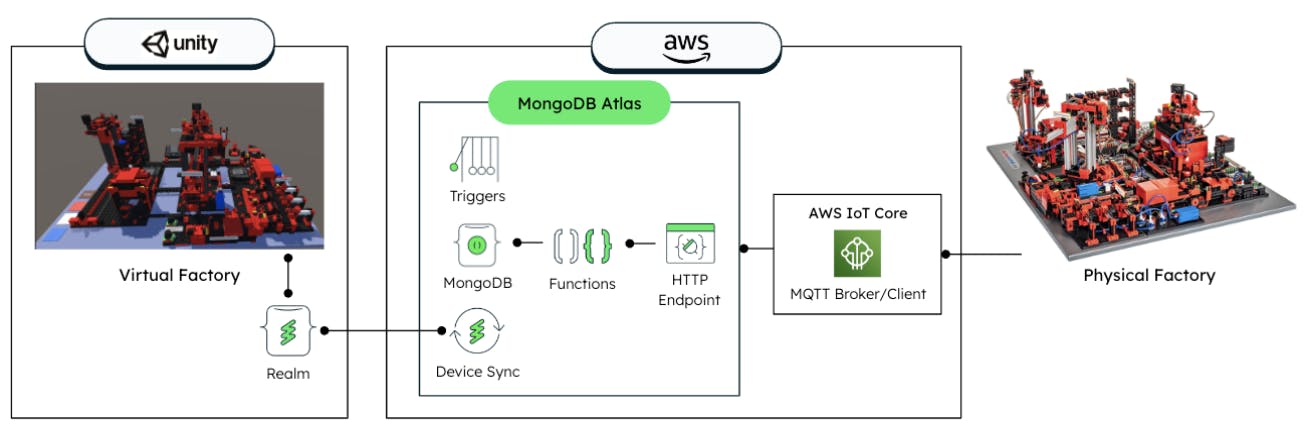
In figure 5, we can see everything we’ve put together so far, on the left hand side we have our virtual factory where users can place an order. The order information is stored inside Realm, synced with MongoDB Atlas using Atlas Device Sync and sent to the physical factory using Atlas Triggers. On the other hand, the physical factory sends out sensor data and event information about the physical movement of items within the factory.
MongoDB Atlas provides the full data platform experience for connecting both physical and virtual worlds!
4. Data modeling
Now that the connectivity has been established, let’s look at modeling this data that is coming in. As you may know, any piece of data that can be represented in JSON can be natively stored in and easily retrieved from MongoDB. The MongoDB drivers take care of converting the data to BSON (binary JSON) and back when querying the database. Furthermore, you can use documents to model data in any way you need, whether it is key value pairs, time series data or event data.
On the topic of time series data, MongoDB Time Series allows you to automatically store time series data in a highly optimized and compressed format, reducing customer storage footprint, as well as achieving greater query performance at scale.
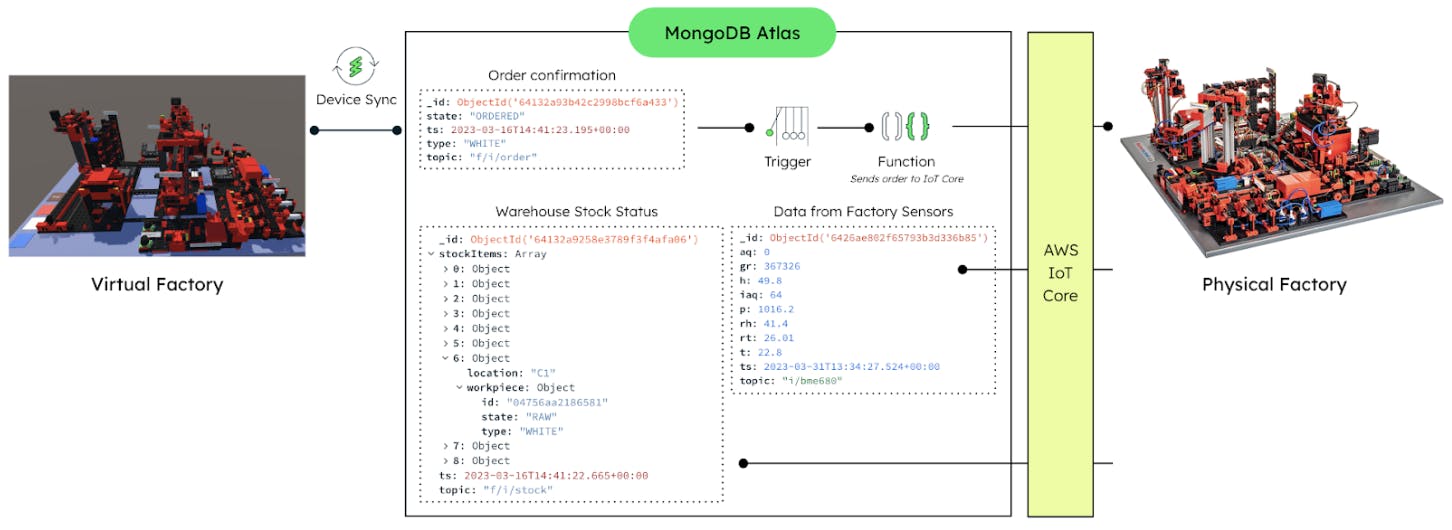
It really is as simple as it looks, and the best part is that we are doing all of this inside MongoDB Atlas making a direct impact on developer productivity.
5. Enable computer vision for real-time inventory
Once we have the data modeled and connectivity established, our last step is to run event-driven analytics on top of our developer data platform. We used computer vision and AI to analyze the inventory status in the physical factory and then pushed notifications to the virtual one. If the user tries to order a piece in the virtual factory that is not in stock, they will immediately get a notification from the physical factory. All this is made possible using MongoDB Atlas and its connectors to various AI platforms
If you want to learn more, stay tuned for part 2 of this blog series where we’ll dive deep into the technical considerations of this last step.
Conclusion
By investing in a virtual factory, companies can optimize production processes, strengthen quality control, and perform cost-effective testing, ultimately improving efficiency and innovation in manufacturing operations.
MongoDB, with its comprehensive features and functionality that cover the entire lifecycle of manufacturing data, is well-positioned to implement virtual factory capabilities for the manufacturing industry. These capabilities allow MongoDB to be in a unique position to fast-track the digital transformation journey of manufacturers.
Learn more: